Nov 16 2017
Case Study: Driver® Generate Downhole Traction
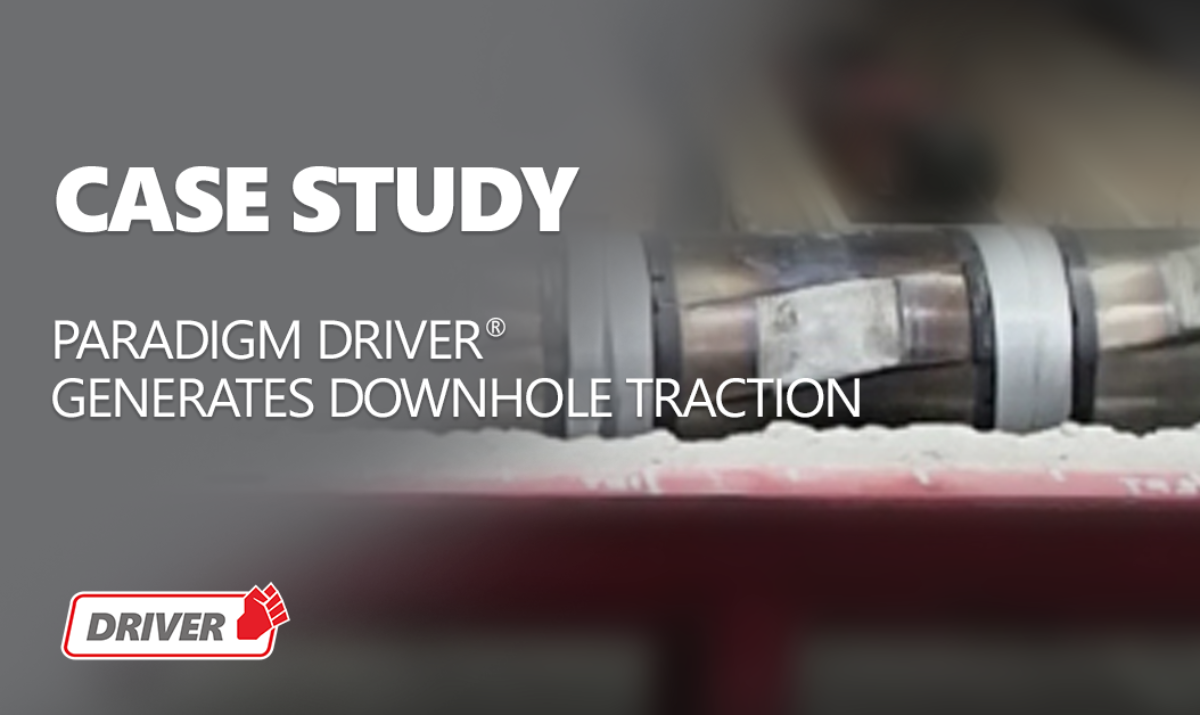
Objective
Two 4 ¾” Driver® tools were introduced to a rotary steerable assembly, directly above the upper NMDC, to evaluate the traction force produced. Data subs were also run to measure the additional WOB, and to see what effect the tools had on vibration within the assembly and at the bit.
Method
A rotary BHA was run, with stabilisers sized and spaced to simulate a typical RSS. Data subs were run at the bit, and at the top of the BHA, and three runs were undertaken to drill 240’, 305’ and 271’ of 6 1/8” Horizontal Hole. The two Driver® tools being introduced into the upper BHA for the middle run of 305’, for comparative measurements. Data Sub measurements were also gathered, at the same depth and 101° of inclination, with and without the Driver® tools whilst rotating of bottom.
Test Results: Driver® Tools Generate Traction
The first BHA; without the Driver® tools; behaved as expected with no weight at the Bit Sub and a compressive force of 1,650lbs at the top of the BHA. The compressive force at the top of the BHA was significantly reduced, and measured just 400lbs, when the two Driver® tools were introduced. Indicating that the Driver® tools were generating 1,250klbf of traction.
Test Results: Traction force contributes to even greater Measured Additional WOB The 1,250lbf of axial thrust, generated within the upper BHA by the two Driver® tools, reduced compressive and torsional buckling in the lower 3 ½” drill string; effectively moving the neutral point lower in the string. Resulting in better weight transfer along the horizontal section, and an increase to actual WOB of 3,000lbs:
Test Results: Lateral Vibration Greatly Reduced Introduction of the Driver® tools significantly reduced vibrations, at the top of the assembly and especially at the bit. The vibration charts clearly show the bit tracking true and smooth, with the Driver® assembly, as the additional 3,000lbs WOB allowed the cutters to properly engage with the formation.